Notes from the Field: The Factories Who Make Our Clothes
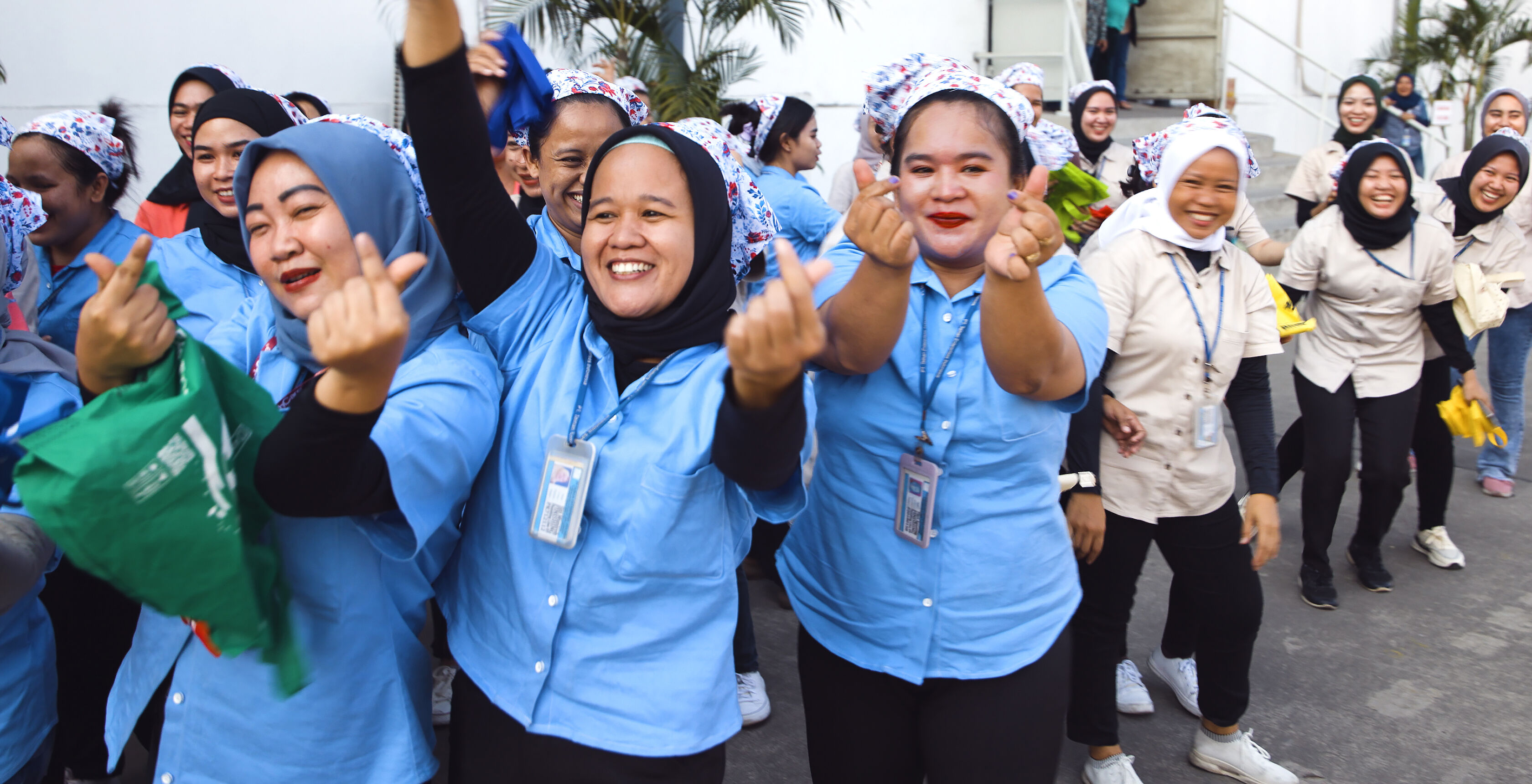
6 factories, 4 cities, 2 countries—and 1 eye-opening journey.
Who made your clothes? Alana Salguero, Director of Copy, traveled with Susan Scow, Sustainability Impact Specialist, and Michael Chung, photographer, to find out. The team flew to Indonesia and Vietnam to tour factories, strengthen relationships and gather stories from workers. The impetus for the trip: In 2022, EILEEN FISHER partnered with Fair Trade USA to help two factories on their journey toward certification. Now, three of our factories are Fair Trade Certified™, which means they meet rigorous environmental standards and support the well-being of workers. This trip was an opportunity to see firsthand the impact of this program—and to learn more about the people and places our clothes touch.
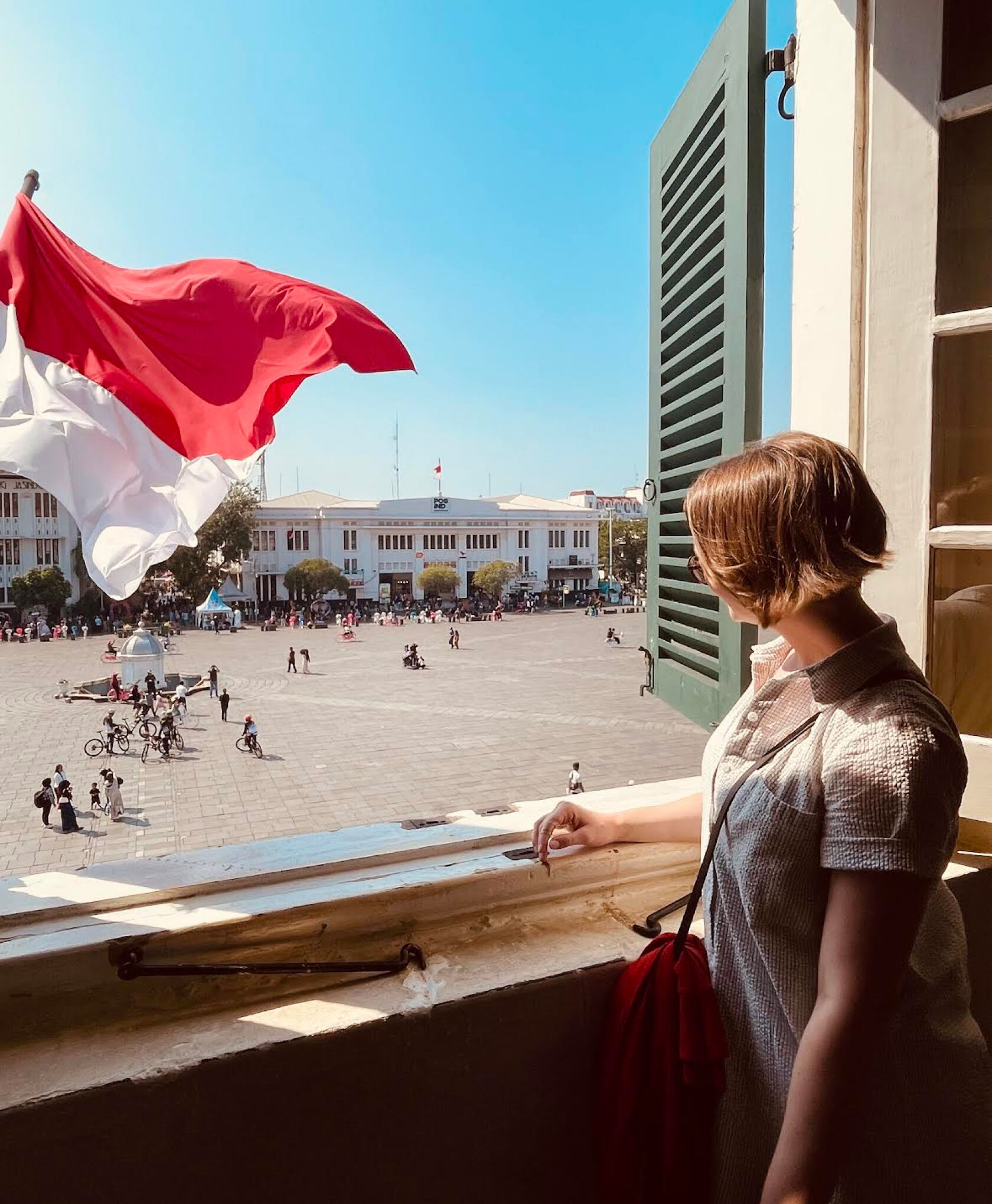
Susan at the Jakarta History Museum, overlooking Fatahillah Square.
DAY 1
Kota Tua, Jakarta
After 35 hours of travel and a rough night’s sleep, the breakfast buffet at the Intercontinental Hotel in Jakarta was a welcome sight. I beelined for the satay and tropical fruit.
In the hotel lobby, we were met by Bu Yolanda and Bu Maria from our sourcing agency. (Ibu or Bu is a respectful address for women in Indonesia; Bapak or Pak is a respectful address for men.) Susan and Yolanda have What’s App-ed, Zoomed and shared pet photos every week since Yolanda joined ERALDA last year, but they’d never met in person—until now.
Together, we drove to Kota Tua (old city) to visit the Jakarta History Museum and see Fatahillah Square. Formerly the heart of Batavia, the square’s many Dutch colonial buildings were festooned with red and white flags in celebration of Indonesian Independence—a complex juxtaposition of history and culture.
DAY 2
PT Tainan (Fair Trade Certified Factory), North Jakarta
Traffic in Jakarta is notorious, but not, in my experience, all that different from rush hour in Manhattan—with considerably less honking. Plus, the one-hour drive to the factory gave us plenty of time for a crash course in Bahasa Indonesia from Yolanda and Maria. The words/phrases that have proven most indispensable: terima kasih (thank you), awas (watch out), panas (hot) and nyamuk (mosquito).
At 10am, we arrived at PT Tainan, a woman-led cut-and-sew factory that produces pieces made from many of our beloved lightweight fabrics (Organic Cotton Poplin, Puckery Organic Linen and Délavé Dyed Organic Linen, to name a few). PT Tainan was one of the first factories that we supported in becoming Fair Trade Certified—and our plan was to spend two days touring the facility and talking to workers about the impact of the program.
I’d visited factories on three continents but had never seen a level of organizational efficiency as I observed at PT Tainan. The warehouse was spotless; the sewing lines ran smoothly. On our factory tour, Reevin Wellington, Merchandising Manager, showed us the very technical way in which workers test fabric torsion. They take a swatch of fabric from different rolls, stitch the panels together, then put the fabric through the wash to see how it torques. This test helps simulate how a garment will perform for the wearer—and ensures that the material meets the highest standards. I asked David Forsgate, Chief Representative Officer of ERALDA Indonesia, if this level of detail was typical in the industry. His response: “Absolutely not.”
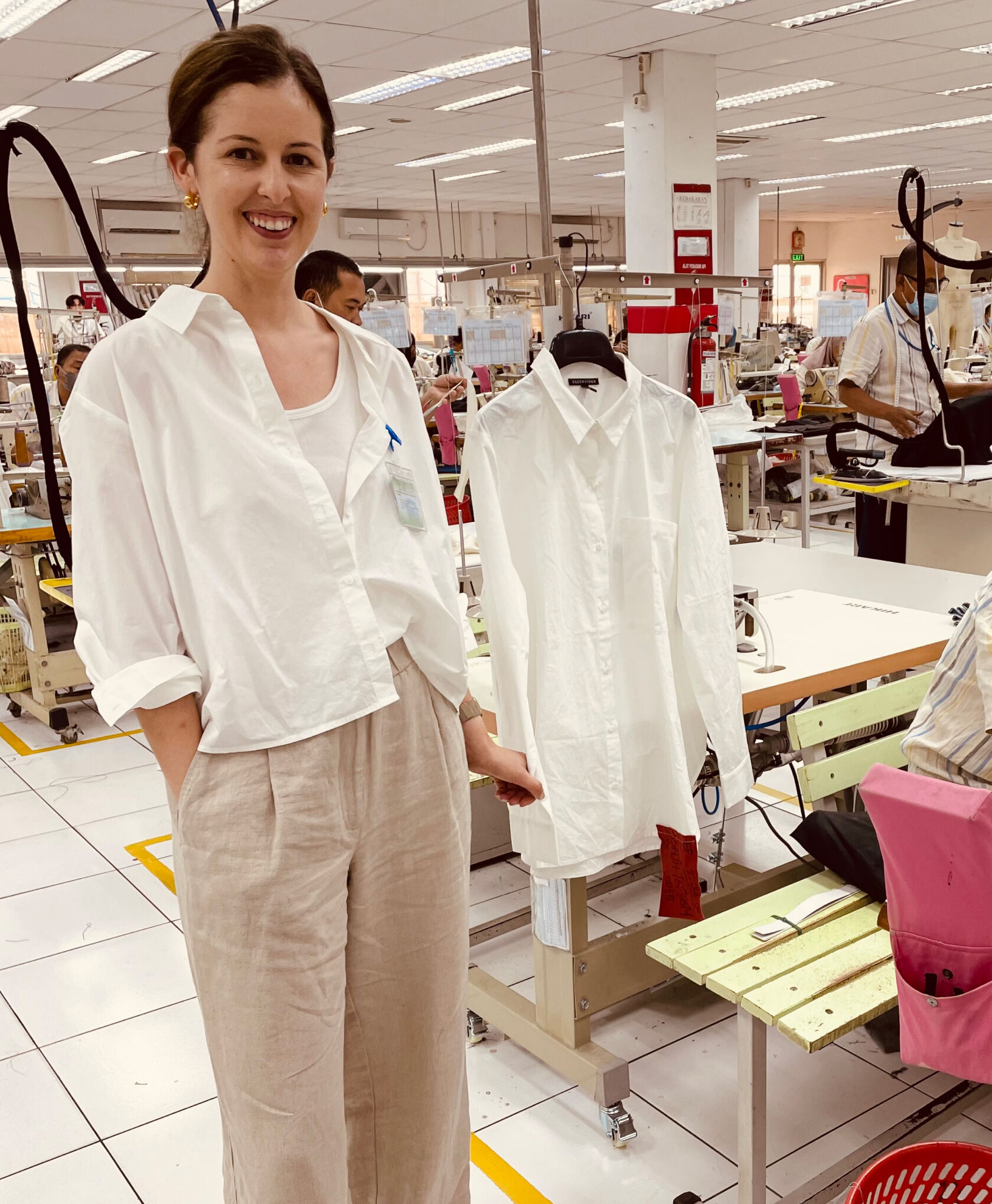
Organic Cotton Poplin shirts are an EILEEN FISHER signature. They’re made at PT Tainan.
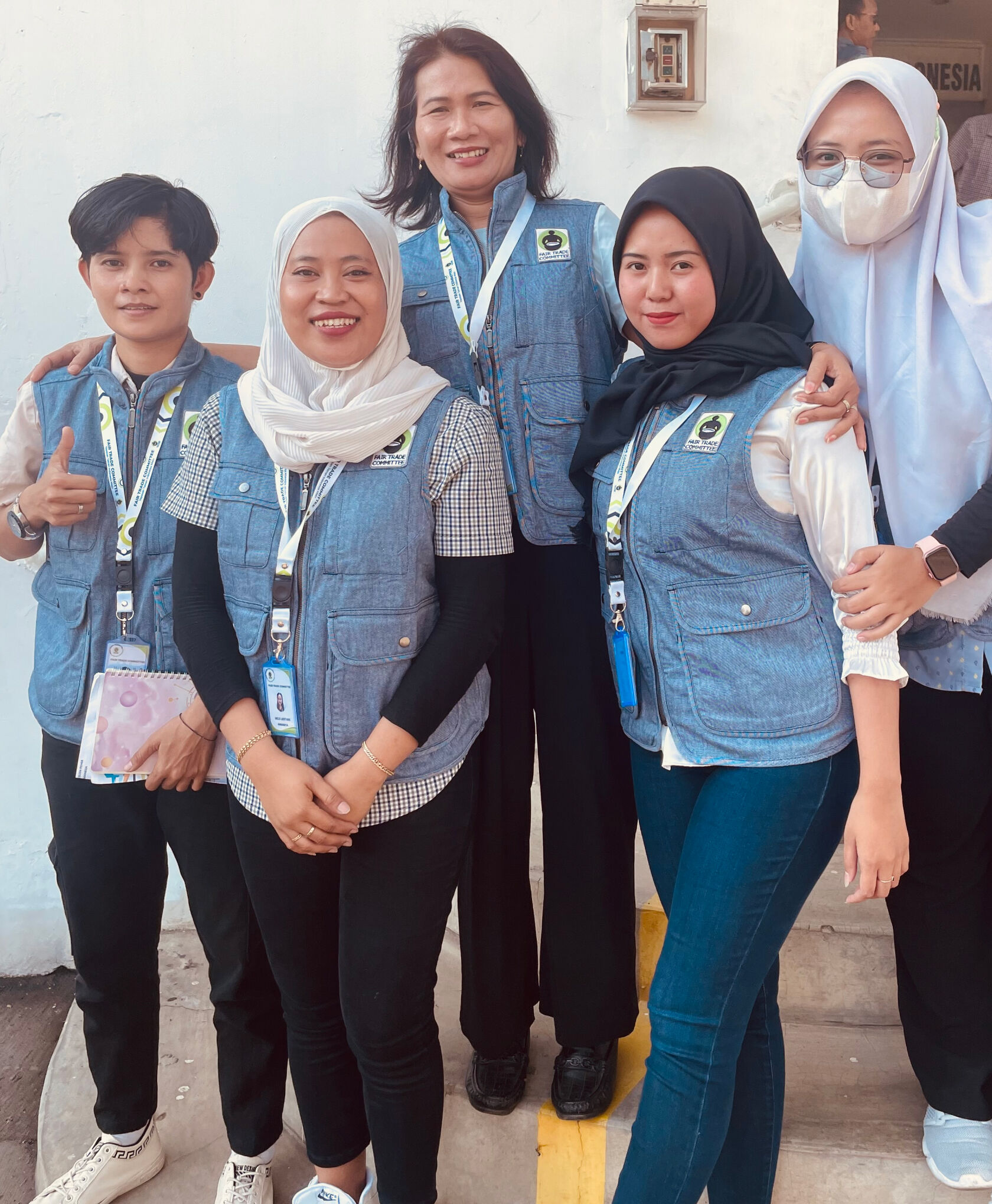
Representatives from the Fair Trade committee, a democratically elected group of employees who support their fellow workers in investing the premium funds.
DAY 3
PT Tainan (Fair Trade Certified Factory), North Jakarta
At 8am, we piled into the car with our trusted driver, Pak Sole—a favorite among the ERALDA staff because of his penchant for playing Guns N’ Roses.
We arrived back at PT Tainan ahead of schedule and took a lap around the industrial complex, passing huge lots stacked high with empty shipping containers. Sending materials and finished garments by boat remains the most sustainable way to move goods across the globe; however, recent conflicts and piracy in the Red Sea have disrupted global shipping routes. That means most brands (including us) are resorting to shipping more goods by air, which has a massive impact on climate health. It’s just another example of how complicated it is to do business in a volatile world.
Our plan for the day was to talk as many workers as possible about their experience with the Fair Trade program. One year after becoming certified, PT Tainan received their first annual premium payment for every Fair Trade garment produced. In June, employees elected a committee to oversee the premium funds and support workers in deciding how to spend the money.
If I’d had to guess how the workers would spend the funds, I would have said individual cash bonuses—that’s likely what I would have chosen myself. In fact, the workers voted to move forward with three different projects: a program to fund free vision care and prescription glasses; financial assistance for school entrance fees; and packages of rice, cooking oil and other pantry staples. The Fair Trade committee told us that many employees chose to share the food they’d received with family and friends or donate what they didn’t need to a local orphanage.
DAY 4
PT Ungaran (Fair Trade Certified Factory), Semarang
We met our ERALDA partners, David and Yolanda, at the airport and boarded a quick flight to Semarang, a port city in Central Java. That afternoon, as we drove to our second factory, Yolanda explained some of the ways Central Java is different from West Java: sweeter food, softer accents.
Turning into the driveway at PT Ungaran, we were met by Pak Arif, Head of Human Resources—we’ve dubbed him “King of Compliance” because of the factory’s incredible social and environmental performance. Year after year, Ungaran continues to improve their score on the Higg Facility Environmental Module (FEM), a tool that helps assess a factory’s water, chemical and energy usage; waste management; and air emissions.
When I asked Pak Arif how he and his team had managed to accomplish this, he explained: “We start by tracking our emissions and usage, which allows us to set a baseline. Once we have a baseline, we turn to goal setting and prioritizing—what five goals do we want to accomplish this year?” A very methodical approach that’s easier said than done. “Pak Arif could teach a master class in the Higg FEM,” added Susan.
Strategic goal setting has allowed Ungaran to achieve Fair Trade certification in record time. After EILEEN FISHER approached Ungaran in April about trading on fair trade terms, the factory underwent a rigorous audit to ensure environmental and social compliance. They passed with flying colors in July, a month before our visit.
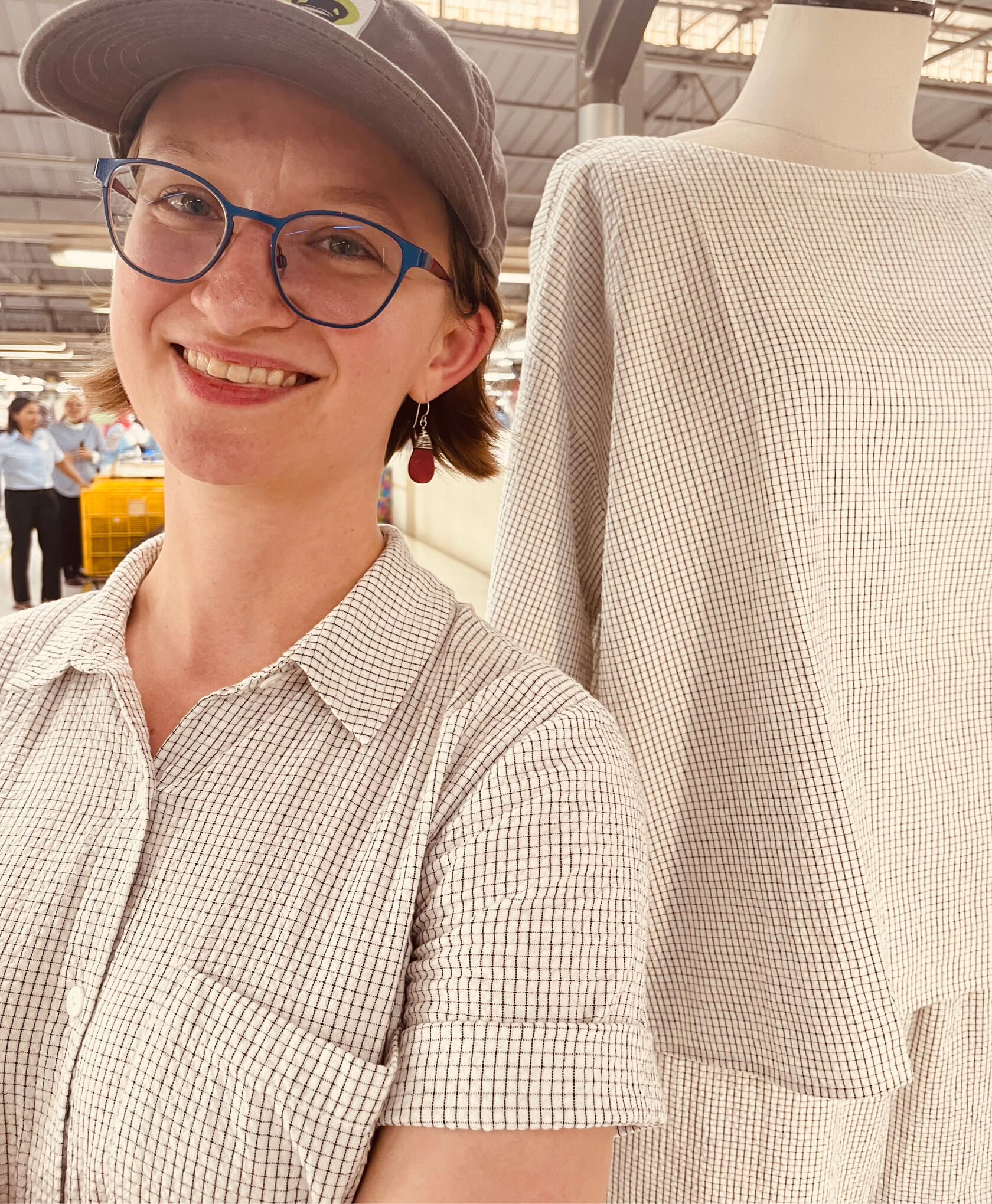
Susan wearing Organic Cotton Ripple, a breezy fabric that's cut and sewn right here at PT Ungaran.
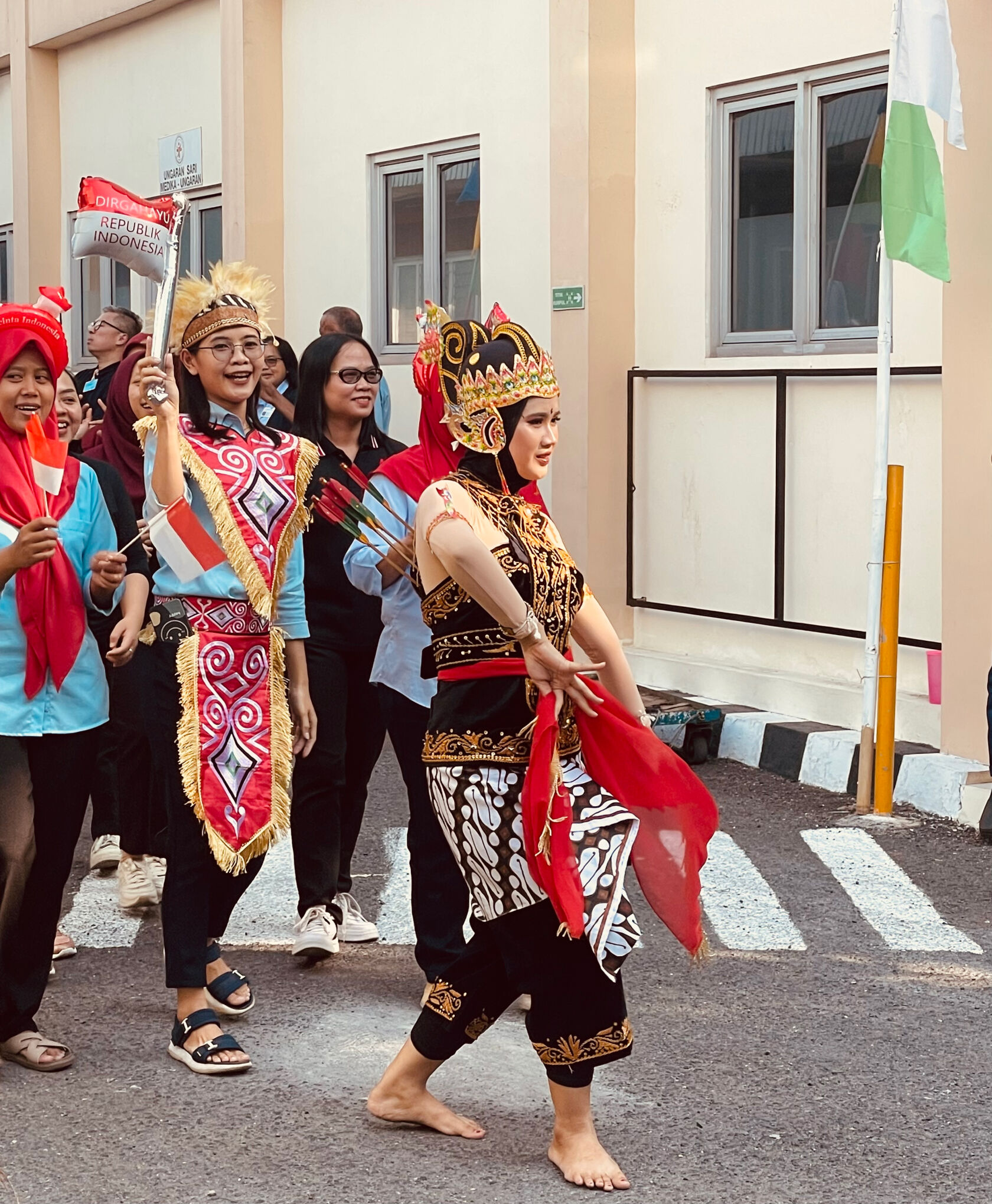
Workers celebrate Indonesian Independence at PT Ungaran.
DAY 5
PT Ungaran (Fair Trade Certified Factory), Semarang
We awoke at dawn, arriving at Ungaran just in time for Michael to power up his drone and capture aerial footage of more than 2,000 workers filing in for their morning shift—an impressive sight, from any vantage point.
Our tour of the facility included a visit to the cafeteria, where chefs were busy preparing sayur gudangan (salad with grated coconut), followed by a two-minute active stretching break designed to get workers up and moving. Later, we sat down with three women—Bu Yuni 1, Bu Yuni 2 and Bu Widyastuti—to talk about their experiences on the production floor. All had worked at Ungaran for more than 30 years. When asked why so many employees held such long tenures, each replied that it was because the factory felt like a second home.
You could feel the sense of community, especially during the afternoon festivities—an annual Independence Day celebration and talent show, featuring singing, dancing and performances. We were given handmade crowns by the quality control team and did our best to follow along with choreographed routines. The laughter and joy were contagious.
The good cheer continued in the company orchard, where I, as a first-time guest, was invited to plant a tree. (Susan planted hers in 2022. It is thriving, I am happy to report.)
DAY 6
Vina Nobland (Fair Trade Certified Factory), North Ho Chi Minh City
We awoke early in bustling Ho Chi Minh City, eager for our first Cà Phê Sữa Đá—Vietnamese iced coffee with sweetened condensed milk. We call it “rocket fuel.”
Gavin Forsgate, Director of ERALDA Vietnam, met us in the hotel lobby and ferried us north to Nobland, a factory that manufactures our Flex Ponte and Woven Plisse. Nobland was one of the first factories we supported in becoming Fair Trade Certified™ in 2023, and we were eager to hear how the program was going a year later. Tony Nam, Head of Environmental & Social Governance, explained that the employee committee had decided to hold a portion of the premium dollars for next year, when the amount of money would make a bigger impact. In the meantime, the group decided to fund a green awareness campaign and purchase towels and reusable jute bags for every worker—a reminder to reduce plastic waste.
Every factory, we learned, has a slightly different culture and feel. At Nobland, workers prefer to eat lunch at the canteen very quickly, then return to the production floor for a 45-minute power nap. I saw one employee hang a hammock between the storage bays to get more comfortable. Another eye opener: the motorbike garage in the basement. Most workers here live an average of 30 minutes from the factory and ride bikes to work. At 4pm, when the bell rings to signal the end of the day, more than 2,000 riders grab their helmets, rev their engines and take off en masse.
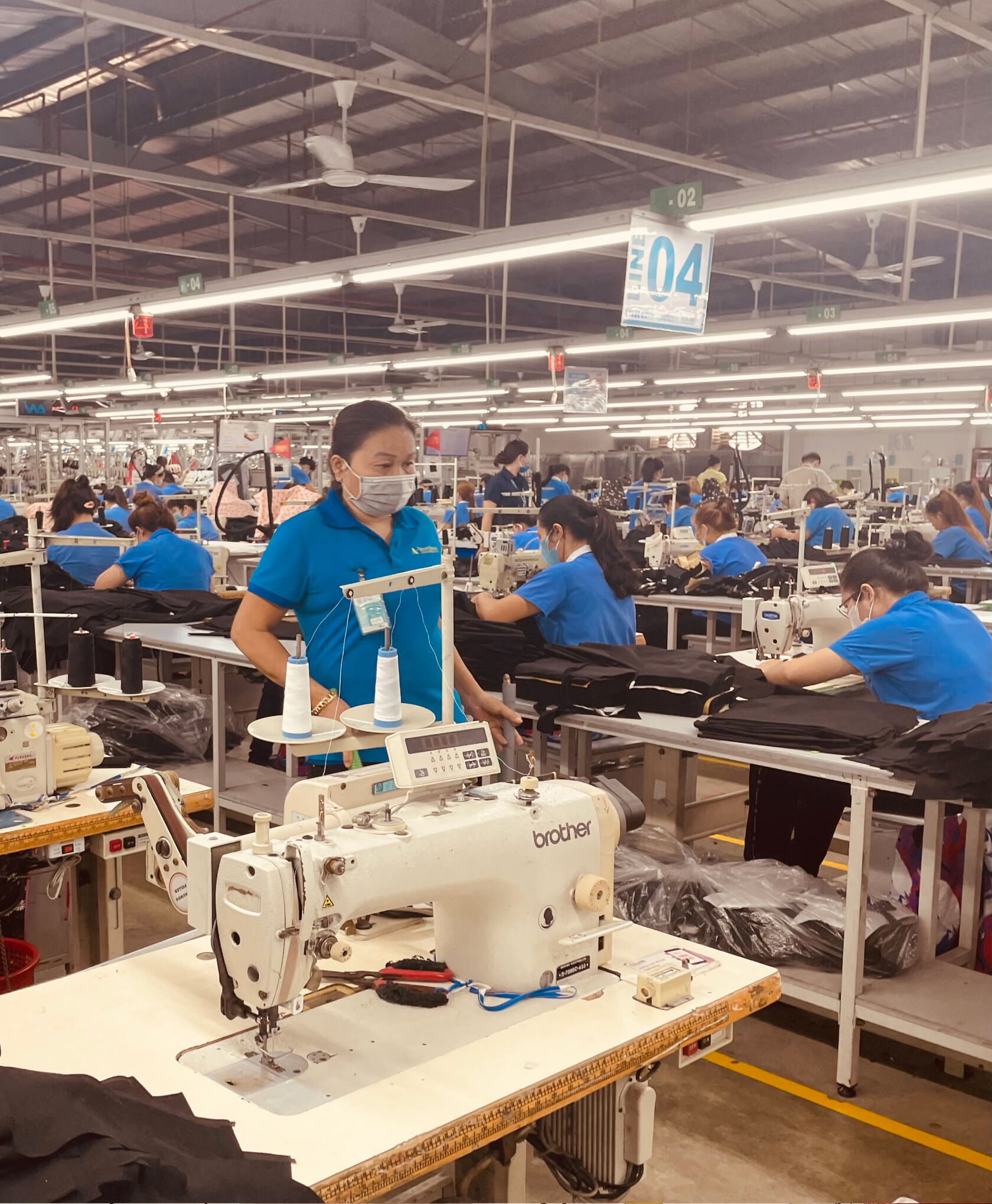
The sewing line at Vina Nobland, a Fair Trade Certified factory outside of Ho Chi Minh City.
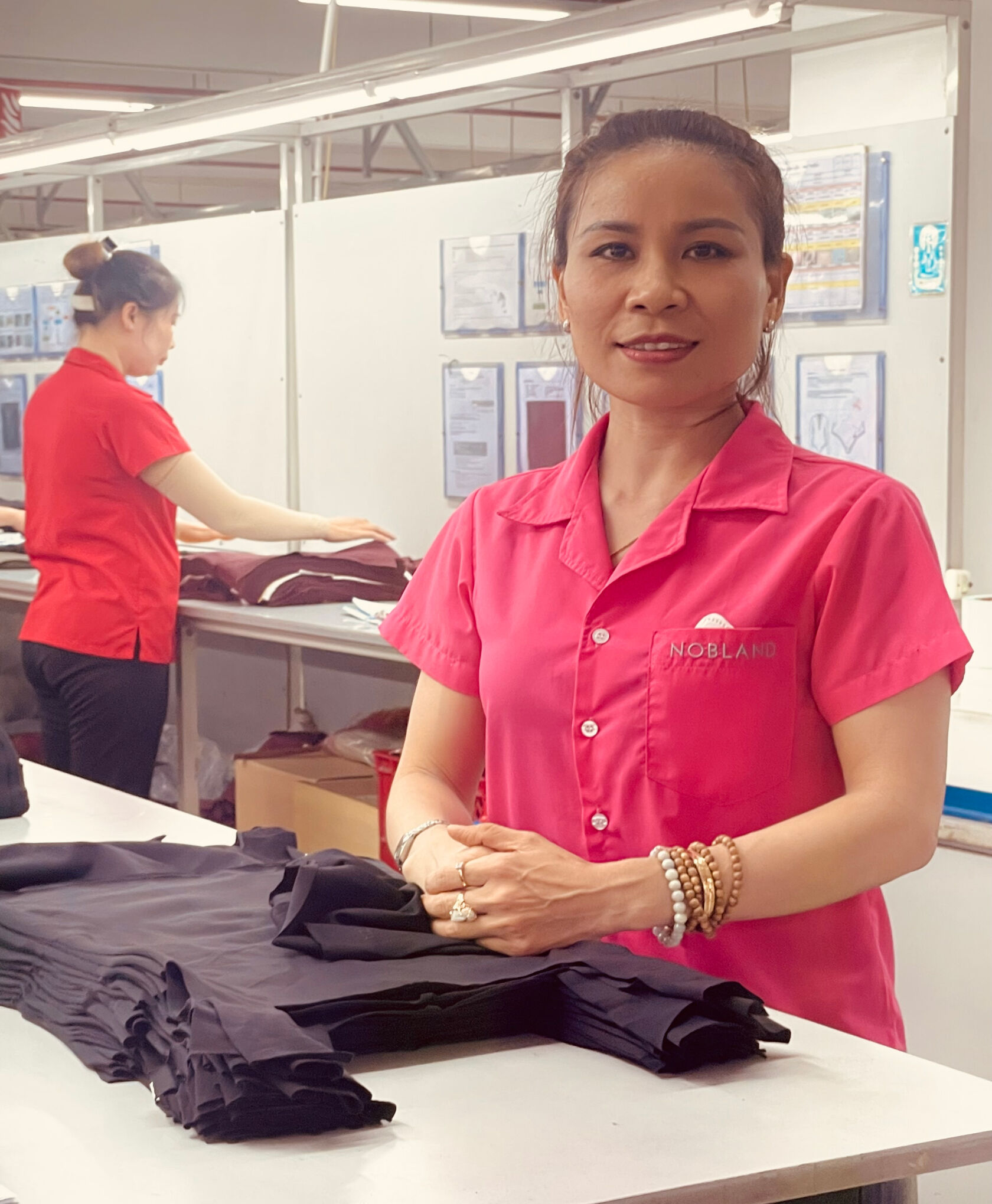
A quality control worker at Vina Nobland.
DAY 7
Vina Nobland (Fair Trade Certified Factory), North Ho Chi Minh City
After a few cups of rocket fuel, we drove back to Nobland to talk to workers about their experience. One Quality Control Manager explained that 99 percent of employees belong to a union, which she credits with helping build positive communication between workers and management. A recent example: Employees wanted rice porridge added to the lunch rotation, so they asked their union leader to make a formal request. It’s now on the menu daily.
Another worker told us that the company benefits she finds most meaningful are the educational classes on topics such as financial well-being and communication skills. “Those communication classes are the reason I am able to talk to you on camera today,” she added.
An added bonus, we had the opportunity of interviewing Tam Dao, a representative from Fair Trade USA who spends six months of the year in Asia supporting factories on their journey. Fair Trade is described as a model for collective change, and I was curious to learn more about what that looks like in practice. “In the first year,” Tam explained, “workers tend to spend premium dollars on smaller-scale projects—cash bonuses or basic necessities like food.” As time goes on, workers often choose to pool their money and invest in programming that benefits the community as a whole, whether that means building an on-site day care, funding medical clinics or installing clean water systems in homes. Critically, workers must vote and decide on the projects—with no input from factory management or brands. That’s because workers know best what their needs and priorities are.
DAY 8
Sick Day, North Ho Chi Minh City
At 8am, our morning call time, I was in bed with the covers over my head.
While I rested in the hotel, the EF team headed to Deutsche Bekleidungswerke (DBW for short), a LEED certified cut-and-sew and knitting factory that produces many of our seasonless sweaters. Susan and Yolanda sent me photos of the modern, light-filled facility and the impressive green roof. The garden helps cool the building—and provides workers with a beautiful space to sit and rest.
In addition to missing the factory tour, I also missed dinner with a very special guest: John Herscher, EILEEN FISHER Director of Quality & Manufacturing Operations, who was in town for a routine quality assurance visit.

Not a garden—it’s a green roof. Susan at DBW.
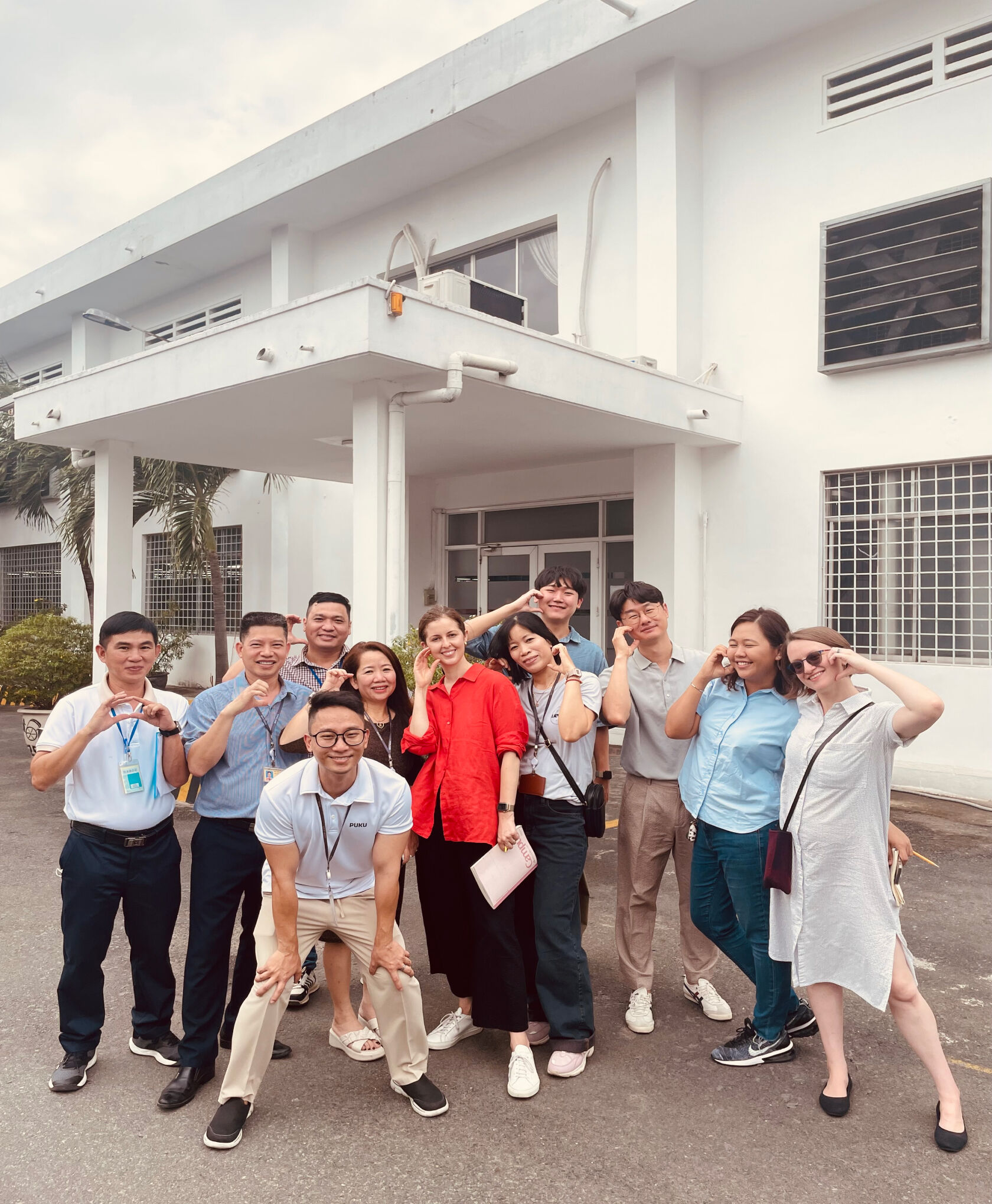
The Environmental & Social Governance team at Puku, a cut-and-sew factory outside of Ho Chi Minh City.
DAY 9
Puku Vietnam Co., Binh Duong
We checked out of the hotel, piled suitcases into the car and drove an hour northeast for a pop-in at Puku.
A cut-and-sew factory that’s owned by the same corporation as Nobland, Puku is currently a small supplier for EILEEN FISHER; however, one never knows when a small supplier may become a bigger one, so it’s always good to visit a facility and get to know your partners. (In this case, that included a meet and greet with Puku, resident guard dog.)
After lunch, we set off for the airport, where it was time to say a goodbye: Yolanda, forever an honorary member of team EF, was returning to Indonesia, and we were off to Hanoi for the final leg of our trip.
DAY 10
Vina Kyung Seung, Phú Thọ
The countryside surrounding Kyung Seung can only be described as scenic: rolling fog, jagged peaks and green fields dotted with small family shrines. Around 10am, we pulled into the factory and were warmly greeted by Liz Oh, Head of Compliance, and her team.
At Kyung Seung, the ambience is one of laid-back focus. I trailed behind Susan and Liz as they walked the floor, eyes scanning to make sure fire lanes remained clear. In the production area, a line of sewers worked on pencil skirts made from our signature Stretch Jersey, part of the pre-spring collection. The quality control team gave each piece a final check before sending them on to be pressed, folded and packed. At Susan’s request, we finished the tour with a visit to the chemical storage shed out back. How do you delight a Sustainability Impact Specialist? Properly segregate your hazardous chemicals.
On the 90-minute ride back to the hotel, the conversation turned to living wage. It’s a difficult topic that raises many questions. How to define a living wage? What methodology should one use to calculate it? Kyung Seung pays its wages according to the Anker Method, one of a few verifiable living wage calculations grounded in math and social science. Methodologies are critical, Susan explained, but it’s important for companies to start their journey by asking themselves, “What do we want the lived experience of our workers to be?”
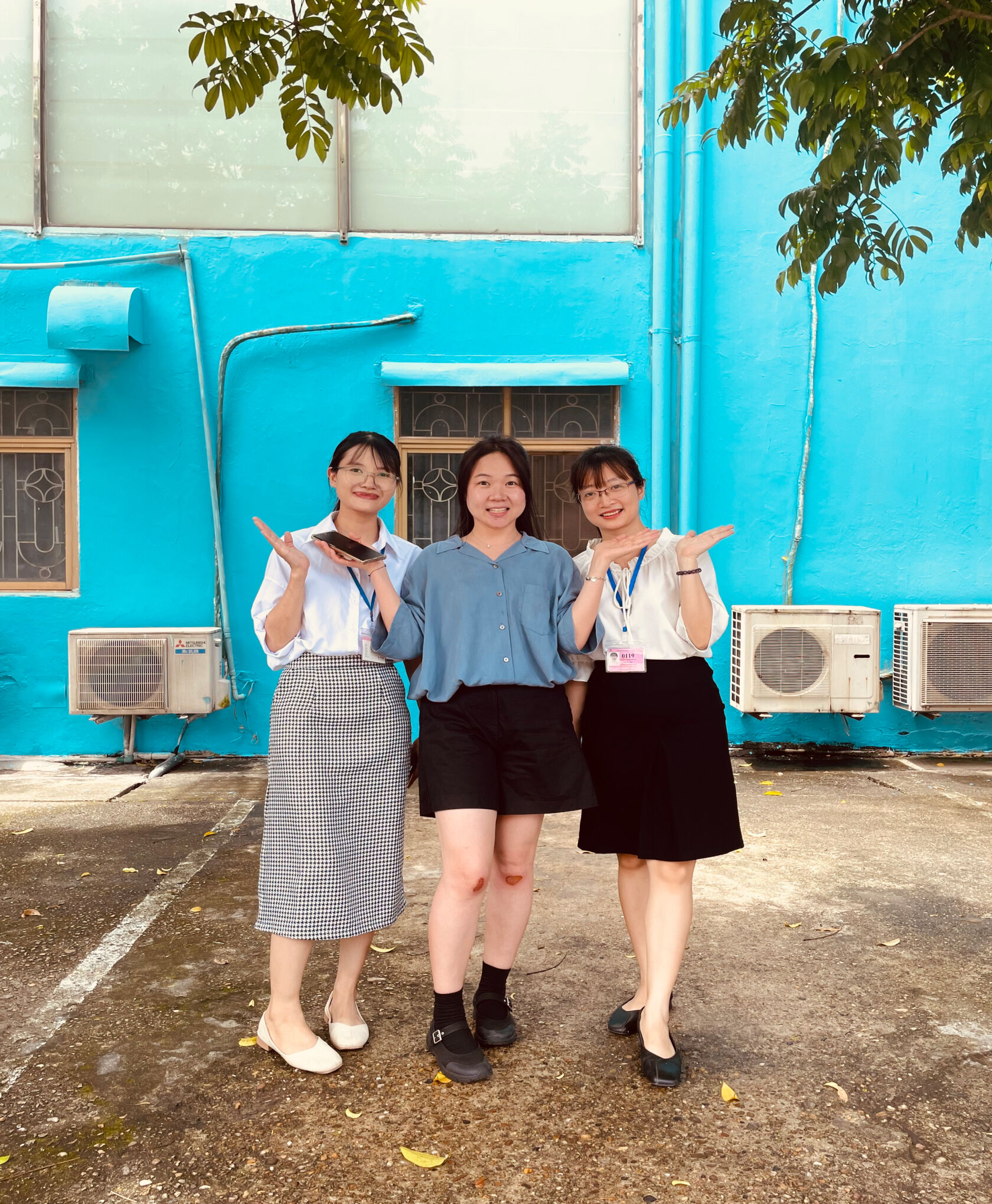
Liz Oh, Head of Compliance (center), and the team at Kyung Seung.
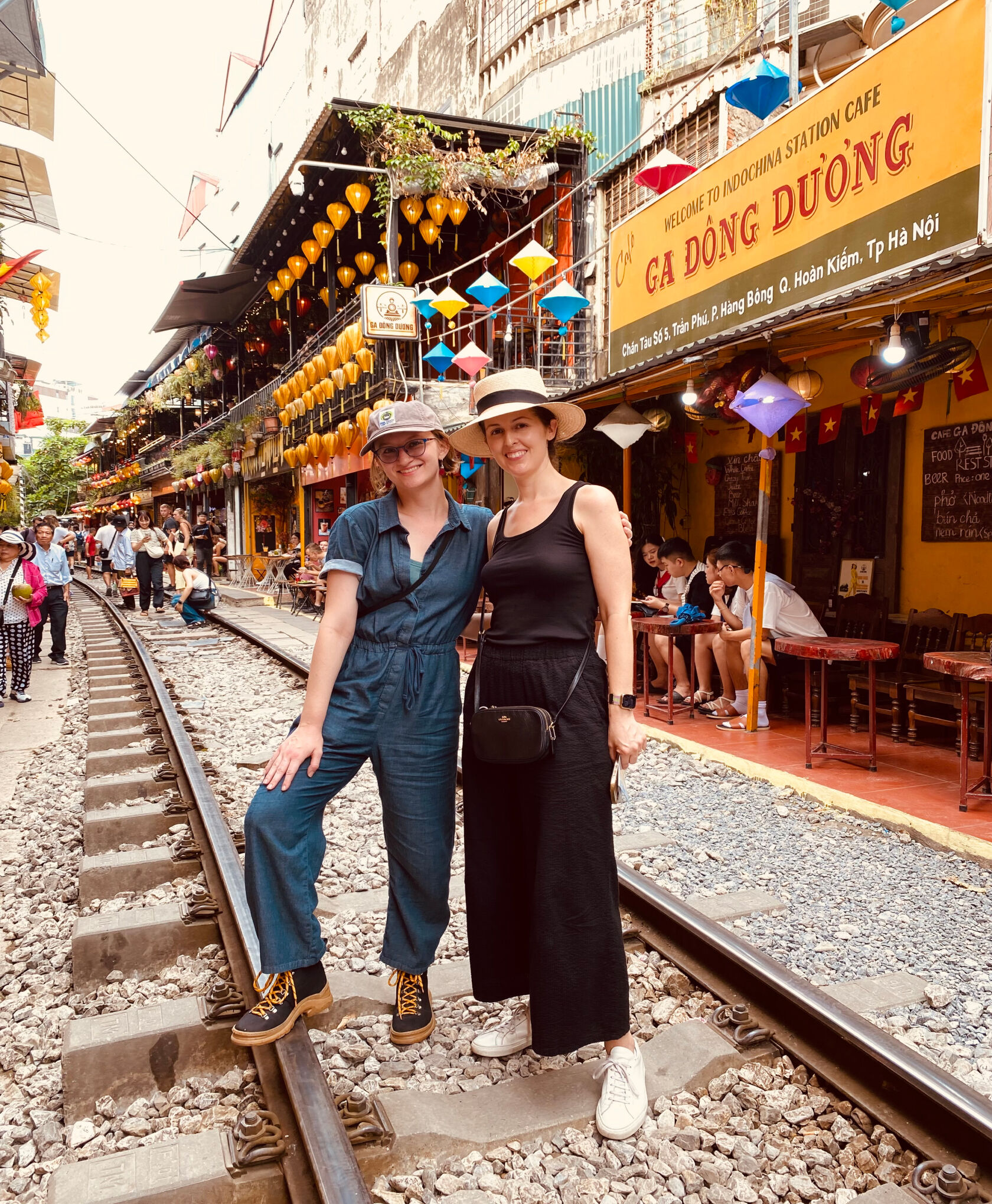
Susan and Alana at Train Street, a narrow alleyway where a train rattles through twice each day.
DAY 11
Old Quarter, Hanoi
On our last morning together, I sat down with Susan on camera to talk about her work in supporting factories through the Fair Trade certification process. “It was mostly paperwork and more paperwork,” she said with a laugh, “but being here and seeing how workers have invested their premiums has given me the biggest rush of joy.”
I also asked a question that had been on my mind: What would you say to people who are skeptical about Fair Trade? Her response confirmed my experience on the trip: Certifications are important, but Fair Trade goes beyond that. Customers can feel confident that workers are receiving premium payments in addition to their salaries and that they are directly benefiting from every Fair Trade Certified garment produced.
Susan ended the conversation with a plea: “We want more brands to join us in trading on fair trade terms. The more brands join, the higher the premium for workers—and the bigger the impact in their lives. It’s truly a win-win for all.”
After wrapping up, we had a full afternoon to explore Hanoi’s Old Quarter— bustling streets, each named after the product on offer. On Silk Street, we admired window displays featuring colorful áo dài, traditional silk dresses. By law, the factories that we partner with in Vietnam must export everything they make overseas. But here, designs are made by locals for a local market, with the quality and craftsmanship Vietnam is known for.
At dinner, our last together before heading to the airport, we toasted to the completion of a successful trip: 14 days, 6 factories, 4 cities, 2 countries—1 fair trade journey that’s far from over.
Goodbyes are never easy, so instead we said sampai jumpa—until we meet again.