How to Spot Quality: The Anatomy of a Seam
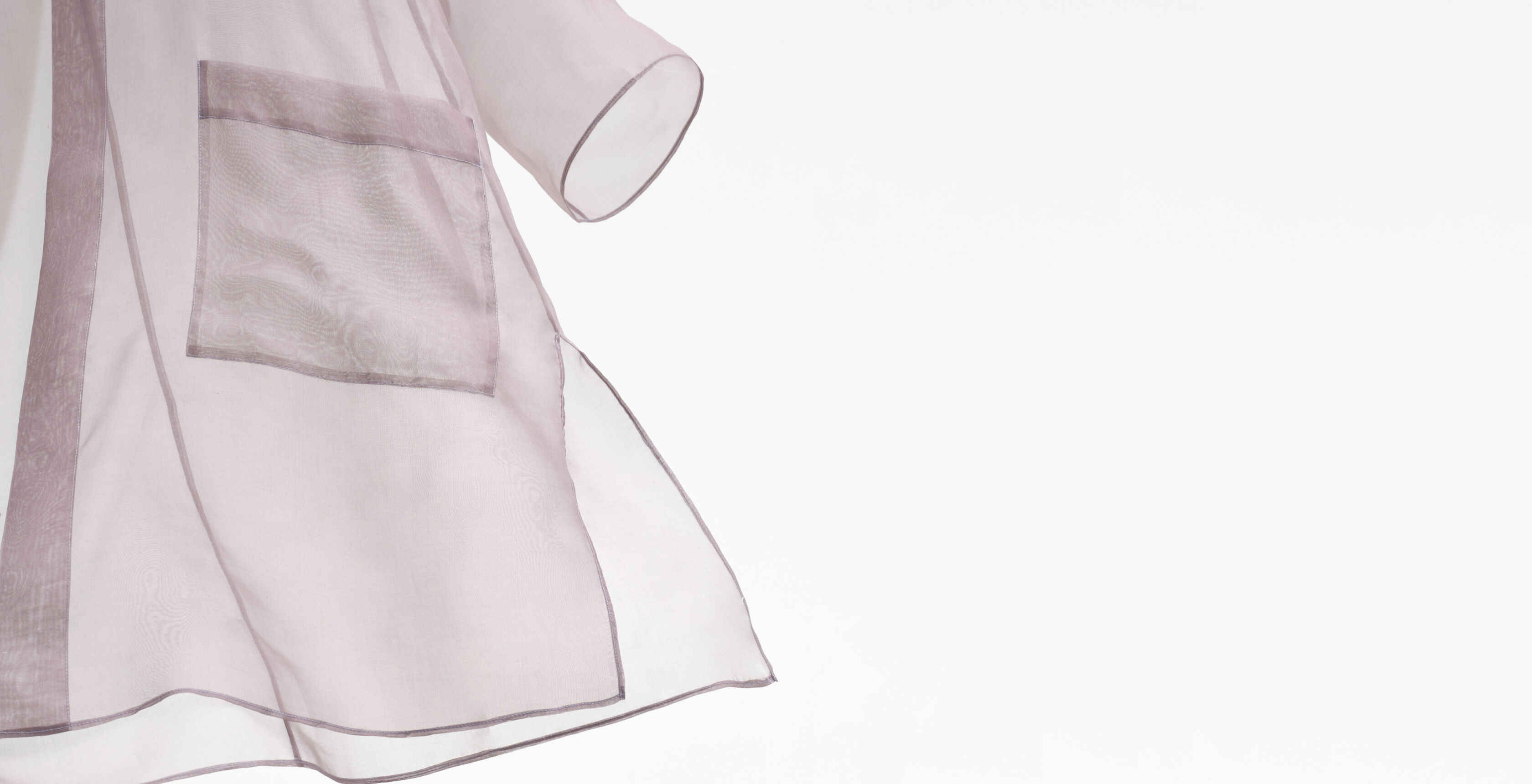
When it comes to seams, there’s a whole lot riding on one little thread—a lesson I learned the hard way.
It all started with an overstuffed suitcase that just wouldn’t close. So I took a deep breath and assumed a “sumo squat.” That’s when I heard the unmistakable ripping sound. Drat. I’d split my pants—and awkward timing, too, since I had to leave my office for the airport in three hours. I wrapped a cardigan around my waist and hightailed it to the nearest tailor, a walk of shame I’ll never forget. As I sat in a tiny changing room, stripped down to my shirt, underwear and socks, I had to ask, where did it all go wrong?
That was before I started working at EILEEN FISHER, where I quickly found out that there’s a lot more to clothing than meets the eye. “Asking what makes a quality garment is kind of like asking what makes food delicious,” says Liz Yager, a former designer in the New York City office. “There are almost an infinite number of factors.” She takes me through the main ingredients: high-grade fabrics, linings, trims, zippers and buttons. But, as in a gourmet dish, the devil is in the details—especially when it comes to garment construction.
Choosing which type of seam to use can be as consequential to a jacket as oven temperature is to a filet mignon. Luckily, our design choices aren’t as limited as they might be at another company. Take the fast-fashion business, where perfection doesn't necessarily lead to profit, and success is driven by low-cost production and speed to market. Product development teams typically have less time and money available to tinker with the details.
‘Choosing which type of seam to use can be as consequential to a jacket as oven temperature is to a filet mignon.’
In Overdressed: The Shockingly High Cost of Cheap Fashion, Elizabeth Cline explains how demanding schedules and budgets have taken their toll on manufacturers. “Many overseas garment factories are very capable of advanced construction techniques, but they also operate on impossibly thin margins and ever-tighter deadlines,” she says. “They do not relish when clients demand a lot of back-and-forth on sampling, testing and perfecting design.”
News like this doesn’t bode well for anyone who prefers to unload the dishwasher while fully clothed. Prognosis: splitsville. At EF, however, every garment is fitted on a person multiple times during the sampling process—and each detail is carefully vetted by several pairs of eagle eyes. Take our silk tank from a few collections ago.
A first sample arrived from the factory finished with “overlock,” an interlocking stitch pattern that’s used to fortify raw edges of fabric at the seam or hem. While this technique works well on lightweight materials with stretch, the product development team opted for French seams instead—a better match for the delicate silk, which could fray if pulled near the stitching.
So how does the layperson tell a quality seam from a future wardrobe malfunction? One key marker is the sewing. Stitching should be consistent, not sloppy or wavering. There is even an ideal ratio of stitches per inch (for a well-made silk tank, expect to see 12 to 14; for a pair of jeans, 9-10). But before you get out your pocket ruler, there’s also the more complex matter of the right seam for the job.
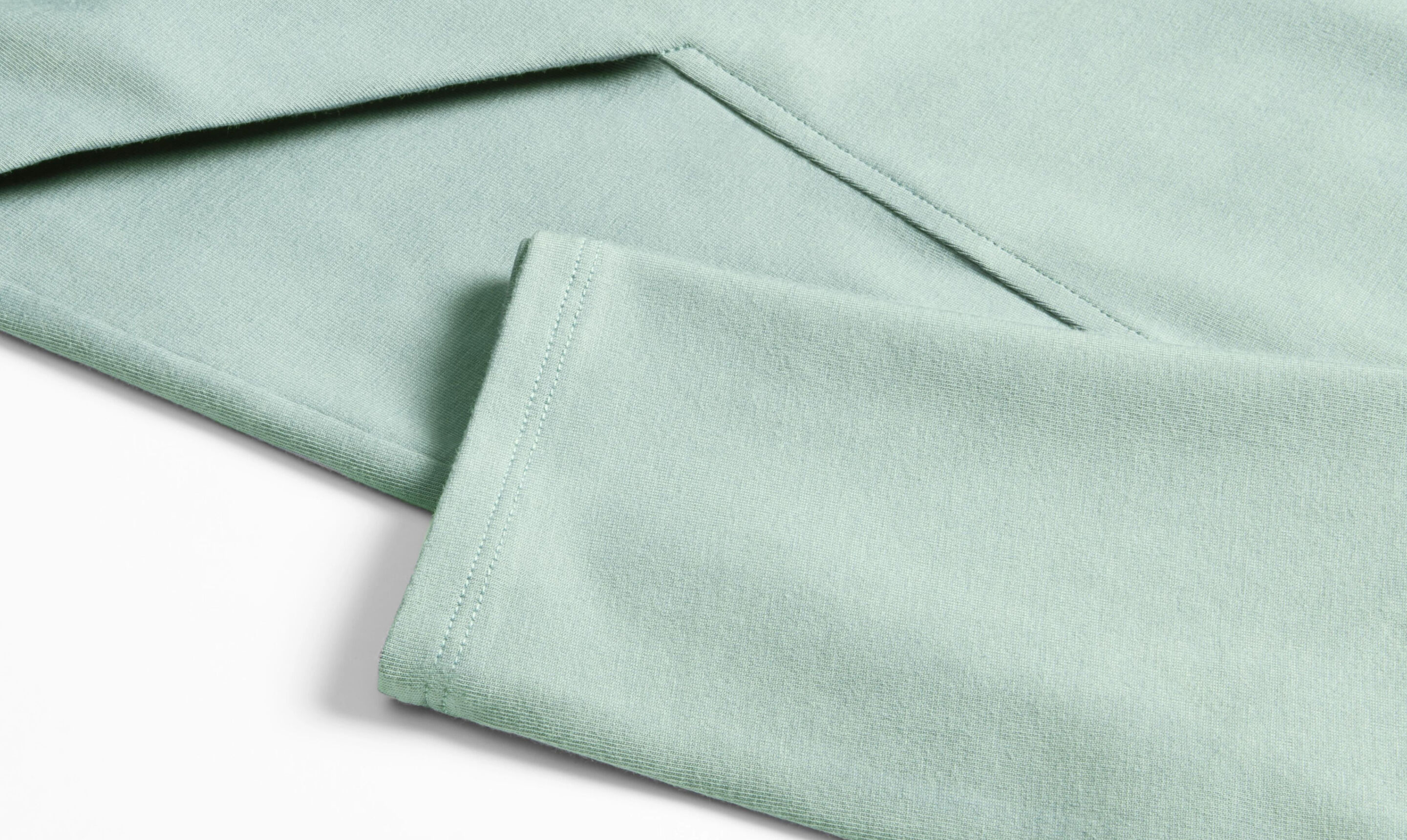
Here are five easy-to-identify techniques that can help you predict whether a seam will hold up when the going gets tough:
OVERLOCK STITCH
This technique requires just one machine to cut the fabric and connect the raw edges with up to five lines of interlocking stitches. Since there are no extra folds, overlock stitching at the seam or hem won’t weigh down a lightweight, stretchy fabric.
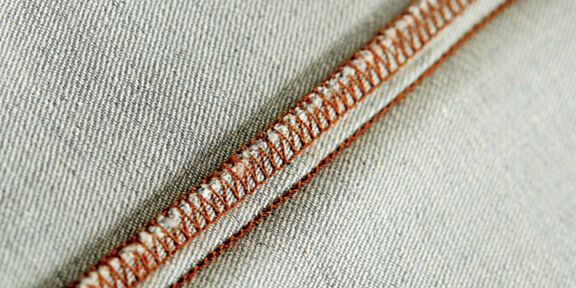
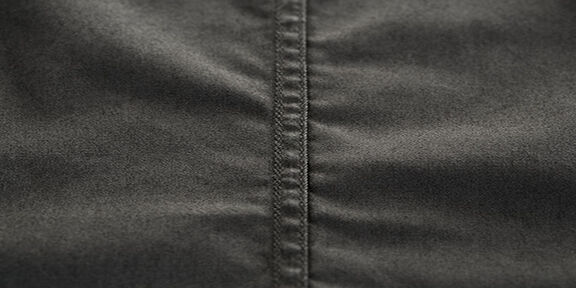
FLAT FELLED SEAM
A favorite for durability, this workhorse seam is stitched, folded over, flattened—and then folded again. The flat felled seam is thick and produces two lines of visible stitching.
CLEAN HEM
A technique commonly used at EILEEN FISHER, the clean hem results in a polished look. You will see stitching one to one and three-quarter inches from the cuff or hem, which has been folded over and pressed.
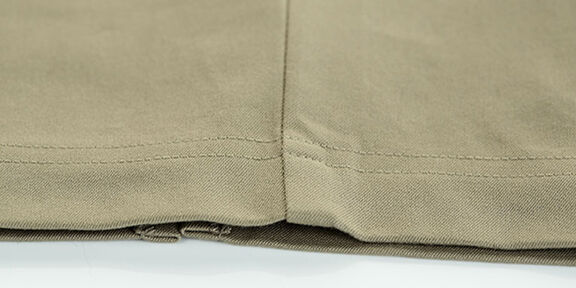
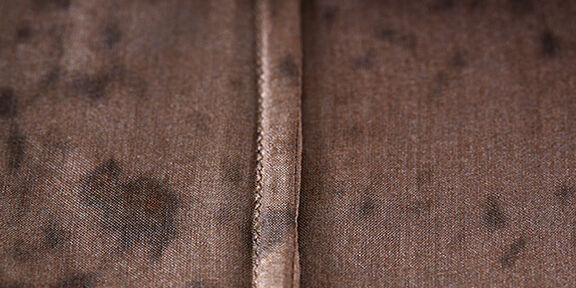
FRENCH SEAM
This finish encases the raw edges within a fold of fabric, hiding most of the stitching for a clean look and soft feel. French seams work well on delicate and gauzy fabrics, which may require an extra line of sewing for reinforcement.
BUSTED SEAM
Contrary to what you may think, this seam actually offers a second line of defense against “busting.” The name comes from the way the two pieces of fabric are sewn together and then pressed open. The raw edges are finished with an overlock stitch, and the extra material allows room for tailoring.
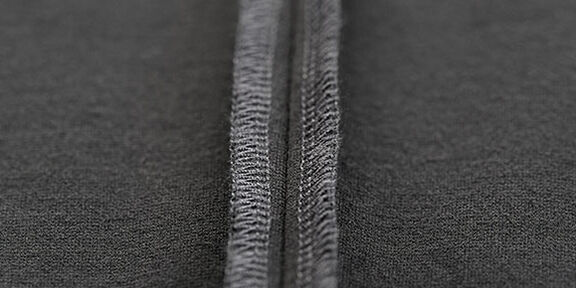